AstraZeneca's Digitally Connected Strategy For API Manufacturing
A conversation with Simon Capewell, AstraZeneca
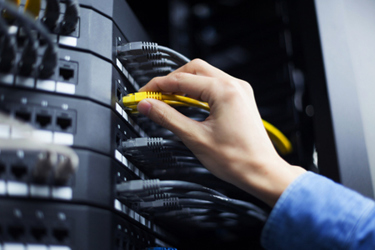
New facility construction gives builders the luxury of packing in the latest technology.
AstraZeneca appears to be making the most of that opportunity with its new API facility for clinical and early commercial supply (APICOM) in Dublin. Construction began in 2023. The company has said it expects construction to conclude around the end of 2025 with an intense focus on data, including its capture, organization, and meaningful deployment at the heart of some of its most advanced technological fixtures.
AstraZeneca’s Simon Capewell, head of operational technology and digital solutions at APICOM, is scheduled to speak about the build during the 2024 International Society for Pharmaceutical Engineering (ISPE) Pharma 4.0 and Annex 1 Conference December 10-11 in Rome along with Simon Webb, a consultant and the founder of Liminos.
Capewell gave us a preview and answered questions about the specific technology they’re using and other aspects of the project.
What are the core design aspects of the project?
In designing our APICOM facility, our ambition was guided by ISA95 principles to establish a connected factory from day one enabled for predictive and adaptive technologies. Building on our Lean foundations of simplified and efficient processes, we have implemented core technology platforms and digital tools to automate and optimize our processes.
A major area of design focus for the facility was the edge architecture (a distributed IT architecture that processes data at the edge of a network). This design will enable us to process the data closer to the source of data generation, such as sensors and equipment on the manufacturing floor, resulting in timely and precise control of processes, which is critical to maintaining product quality and operational efficiency. To complement this, the design of a digital core acts as the central nervous system of the facility, integrating various digital tools and technology platforms to ensure seamless data flows. By implementing these design elements, the facility can achieve streamlined operations, faster response times, and a solid foundation for future technological innovations.
In a project of this magnitude, how do you navigate unexpected changes or issues while maintaining momentum?
Having a clear north star — in this case AI-powered drug development, autonomous manufacturing, and self-healing supply chains — that we are all aligned to, a focus on our strategic purpose, and a robust risk management methodology, where mitigations are actively managed, ensures we engage the workforce through the ultimate mission to deliver medicines to patients.
When navigating challenges, we utilize our supply system framework. This framework integrates Lean principles and problem-solving approaches, which are instrumental in addressing such situations. This is also supported by a company-wide speak-up culture where we encourage learning and continuous improvement through feedback.
For APICOM, which incorporates state-of-the-art processing technologies and digital innovation to expedite the production of small molecules for high-value-added medicines in AstraZeneca’s pipeline, we approach change by emphasizing real-time problem-solving.
What role will AI and advanced analytics play in optimizing production processes, predictive maintenance, and real-time quality control in the new facility?
APICOM has been designed as a digitally connected facility, integrating core technology platforms such as S4/HANA, PAS-X, DeltaV, and a Unified Namespace (UNS) serving as the digital core for the Internet of Things. To enhance our digital maturity and transition toward a predictive manufacturing environment, we are incorporating advanced tools such as digital twins, process analytical technology (PAT), and visualization applications.
As AI technologies mature and regulatory frameworks evolve, we plan to implement machine learning and advanced process control (APC) on our continuous API manufacturing lines. These innovations will position us at the adaptive level of digital maturity, where systems dynamically respond to real-time data to optimize operations. Building on insights gathered from tools like digital twins, data modeling, PAT, and APC, we will continue introducing data-driven enhancements across the facility.
Our ultimate goal is to leverage AI and advanced data analytics to drive greater efficiency, enhanced reliability, and superior quality. This journey begins by designing a digitally connected facility, advancing to a predictive operation, and ultimately achieving a fully adaptive manufacturing environment.
What green initiatives are in store to reduce energy and water consumption and waste production?
To reduce energy consumption, we have implemented several key initiatives. This includes optimizing our HVAC systems with airside heat recovery, reduced air changes, and demand control ventilation for non-critical areas. Additionally, we have focused on energy optimization by targeting low specific fan power and implementing energy sub-metering to closely monitor and manage energy usage. Our eHeat initiatives, such as electrifying hot water heating, utilizing heat recovery systems, and limiting the use of steam to specific high-temperature applications, further contribute to our energy reduction goals.
In terms of water conservation, we have introduced various water efficiency initiatives. These include low-flow domestic users, AHU condensate collection for toilet flushing, and a focus on increasing the cycles of concentration in our cooling towers.
To address waste production, our facility has prioritized waste management strategies to minimize environmental impact. This includes diverting over 75% of construction waste away from landfills, establishing a central area for waste recycling and segregation, and embracing modularization and off-site construction methods to reduce waste generation. These efforts align with our goal to promote a circular economy and reduce the environmental footprint of our operations.
Overall, our green initiatives encompass a comprehensive approach to sustainability, integrating energy efficiency, water conservation, and waste reduction throughout our facility. By implementing these initiatives, we are dedicated to achieving our sustainability goals and contributing to a more environmentally responsible and resource-efficient operation.
About The Expert:
Simon Capewell leads the digitalization strategy for API manufacturing platforms, ensuring alignment with AstraZeneca’s Smart Factory initiatives at the company’s APICOM facility in Dublin. With over 27 years of experience in the life sciences industry, he has expertise in program management, API and biopharma manufacturing, OT engineering, supply chain management, and digital transformation. He is a member of the International Society for Pharmaceutical Engineering and holds a degree in mathematics from De Montfort University in Leicester, U.K.